К действиям в тропических условиях подводная лодка оказалась не приспособленной по следующим причинам:
- отсутствие системы кондиционирования в отсеках ПЛ (температура воздуха за бортом превышала 30 С);
- отсутствие системы охлаждения аккумуляторной батареи при её зарядке;
- высокая влажность в отсеках и соленость забортной воды.
Температура на отдельных боевых постах ( электриков, мотористов) доходила до 65 градусов. Всё это приводило к выходу из строя материальной части (засоливанию водяных холодильников, снижению сопротивления изоляции систем, разгерметизации кабельных вводов, коррозийному износу трубопроводов и рубашек охлаждения нижних газовых захлопок и др.)
В 5-м отсеке в рубашках охлаждения внутренних ручных захлопок газоотвода дизелей появились свищи. Для проведения ремонтных работ в море, на ПЛ, в базе, был подготовлен нештатный корабельный электро- и газосварщик из числа личного состава. Это был командир отделения электриков старшина 1-ой статьи В.Нефёдов.
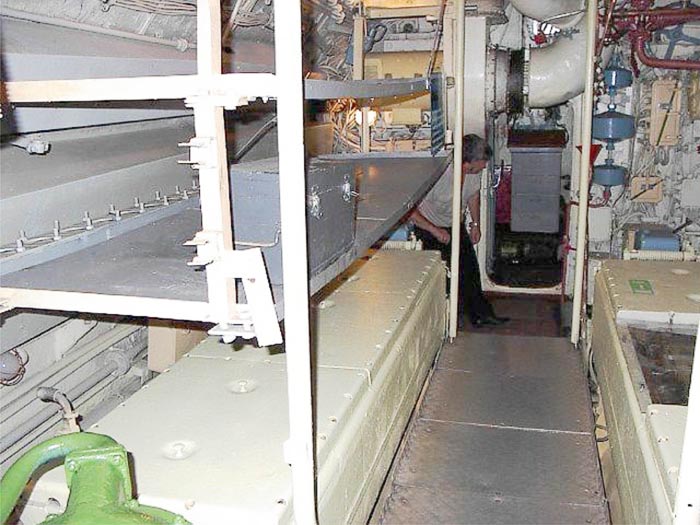
Из-за опасности быть обнаруженными, огневые работы в
Следующей неисправностью, с которой столкнулись электрики в 6-м отсеке, были многочисленные свищи, которые появились на тонкостенных красномедных трубопроводах, подающих забортную воду насосом ВЦН-90 5 отсека к воздухоохладителям ГГЭД.
На подводной лодке установлены три главных гребных электродвигателя. На средней линии вала - ГГЭД типа ПГ-102, мощностью 2700 л.с. при 540 об/мин, на бортовых - ГГЭД типа ПГ-101, мощностью 1350 л.с. каждый при 440 об/мин. Размещались они в 6 отсеке, а ГЭД экономического типа ПГ-104 мощностью 140 л.с. при 185 об/мин размещался в 7-м отсеке на средней линии вала.
Для искусственного охлаждения ГГЭД каждую бортовую машину обслуживал один электровентилятор, а среднюю - два. Производительность каждого - 16000 м3/час.
Воздух от вентиляторов после охлаждения внутренних частей ГГЭД по воздухопроводу поступал в воздухоохладители, откуда попадал в отсек и понижал температуру в нем. В 6-м отсеке установлены восемь воздухоохладителей, по два - на бортовых ГГЭД и четыре - на среднем.
При отсутствии такого охлаждения температура обмоток якорей и полюсов достигает величины критической для материала изоляции, температура воздуха в отсеке становится недопустимой и дальнейшая эксплуатация машины станет невозможной. Например, при выходе из строя двух воздухоохладителей у бортового ГГЭД, его нагрузка должна быть снижена до 75% номинальной (согласно НБИТС-ПЛ), а у нас вышли из строя все восемь воздухоохладителей, так как все трубопроводы, подводящие к ним забортную воду, были в свищах. Для заделки этих свищей были использованы все ленточные бугели, имевшиеся в отсеках подводной лодки, а также резина и аварийная проволока, с помощью которых заделывались свищи на трубопроводах методом клетневки.
Однако аварийных средств для заделки вновь появлявшихся свищей не хватало, поэтому ГГЭД приходилось эксплуатировать с определенными ограничениями. Все это привело к тому, что температура в отсеке приближалась к 70°С, но электрики 6-го отсека мужественно и стойко держались. Бдительно несли ходовую вахту и не прекращали заделки свищей в трубопроводах. Здесь отличились все электрики, несущие вахту в 6-м отсеке. Но особую похвалу и благодарность заслуживают старшина команды электриков главный старшина С.Мухин и командир отделения электриков старшина 1 статьи В.Нефедов.
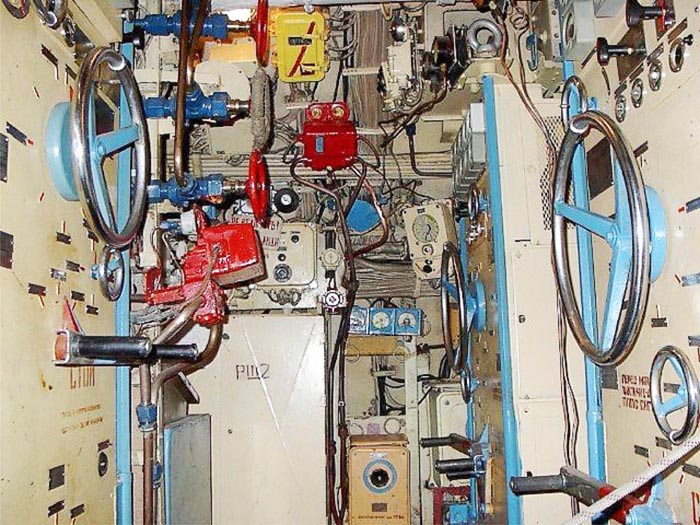
Из-за негерметичности трубопроводов охлаждения ГГЭД в трюме 6-го отсека постоянно накапливалась забортная вода, что увеличивало дифферент ПЛ на корму. Для откачки этой воды почти непрерывно работал осушительный поршневой насос 2П-1 7-го отсека, который грамотно обслуживал старший трюмный старший матрос А.Кондратьев. Повышению температуры в 6-м отсеке способствовала также работа двух электродистилляторных установок типа ЭД 25/45, с помощью которых трюмные из морской воды производили дистиллированную воду. Эту воду использовали для доливки в электролит АБ, а также для восполнения недостававшей пресной воды личному составу ПЛ. С помощью этих установок трюмные произвели более 10 тонн дистиллированной воды. Необходимо отметить мастерство и отличное знание данной установки командиром отделения трюмных старшиной 1-ой статьи С.Козыревым и старшим трюмным старшим матросом А.Кондратьевым.
Из-за частых всплытий и погружений подводной лодки, зарядок и подзарядок АБ сильно расходовался запас воздуха высокого давления, который при любой возможности пополнялся двумя дизель-компрессорами ДК-2, расположенными в корме 5-го отсека за дизелями, и одним электрокомпрессором ЭК-15, расположенным в 6-м отсеке.
Из-за повышенной влажности воздуха в отсеках постоянно выходили из строя дизель-компрессоры. Причиной этого явились частые поломки всасывающих и нагнетательных клапанов разных ступеней. В стесненных условиях, при высокой температуре в 5-м отсеке, трюмные разбирали компрессоры и заменяли вышедшие из строя клапаны новыми, после чего компрессоры вновь использовали по назначению. За выполнение этих работ большой похвалы заслуживают старшина команды трюмных главный старшина В.Лизунов, командир отделения трюмных старшина 1 статьи С.Козырев и старший трюмный старший матрос А.Кондратьев.
Из-за напряженной обстановки аккумуляторная батарея обслуживалась с нарушениями требований «Правил ухода за аккумуляторными батареями подводных лодок ВМФ» (ПУАБ-64). Аккумуляторная батарея не имела системы охлаждения электролита, поэтому во всех случаях заряд АБ должен быть немедленно прекращен без прекращения искусственного вентилирования АБ при достижении температуры электролита 47°С. Но мы продолжали заряд АБ, так как в подводном положении подводная лодка должна быть обеспечена любой скоростью хода, а для этого аккумуляторная батарея должна иметь полную ёмкость. Для снижения температуры электролита почти постоянно работала система механического перемешивания электролита (МПЭ), что увеличивало расход воздуха высокого давления.
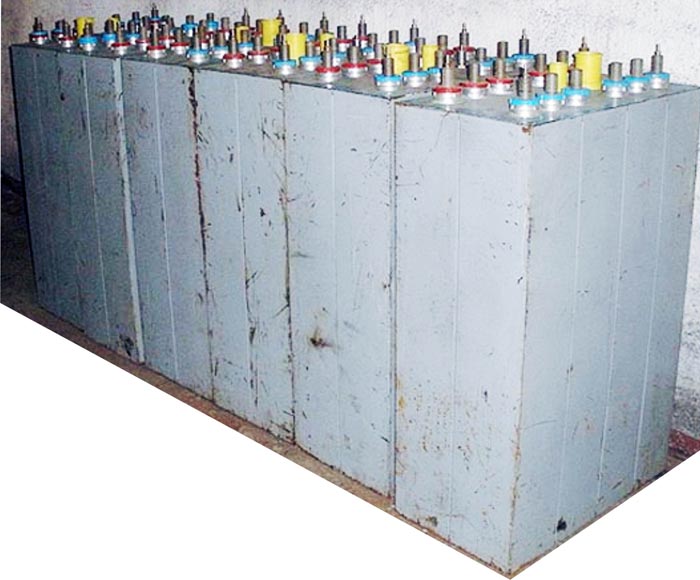
При зарядке АБ в нормальных условиях МПЭ включают:
а) на 15 минут в конце каждого второго часа заряда на всех 3-х ступенях, кроме последней;
б) на 15 минут в конце каждого часа последней - 4-й ступени заряда;
в) на 15 минут перед окончанием заряда, однако для АБ без СВО допускается непрерывная работа системы МПЭ на последней ступени нормального и форсированного зарядов.
При проведении зарядки АБ, электрики контролировали не только температуру электролита, но и концентрацию водорода. Чем выше температура электролита, тем интенсивнее увеличивается выделение водорода. Например, при повышении температуры электролита от 20°С до 40°С на каждые 10°С выделение водорода увеличивается примерно в два раза. А концентрация водорода в воздухе свыше 4% (по объему) образует опасную взрывчатую смесь, которая легко воспламеняется от открытого пламени, от искры любого происхождения, при контакте с любой поверхностью, нагретой до температуры 330°С.
Контроль содержания водорода осуществлялся переносными газоанализаторами. При этом электрики четко знали, что при достижении концентрации водорода в аккумуляторных ямах 3%, заряд АБ должен быть немедленно прекращен без прекращения её искусственного вентилирования. А если подводная лодка вынужденно погрузилась, то электрики начинали вентилировать АБ батарейными вентиляторами в аккумуляторные отсеки при включенных приборах КПЧ-6.
В отдельных случаях температура электролита достигала +65°С, но ни одной аварийной ситуации электрики не допустили. Слава им и хвала! Но особенно хочу отметить грамотную эксплуатацию аккумуляторной батареи командирами отделений электриков старшиной 2 статьи А.Колобовым и старшиной 2 статьи В.Лебедевым.
Однако аварийная ситуация не обошла нас стороной.
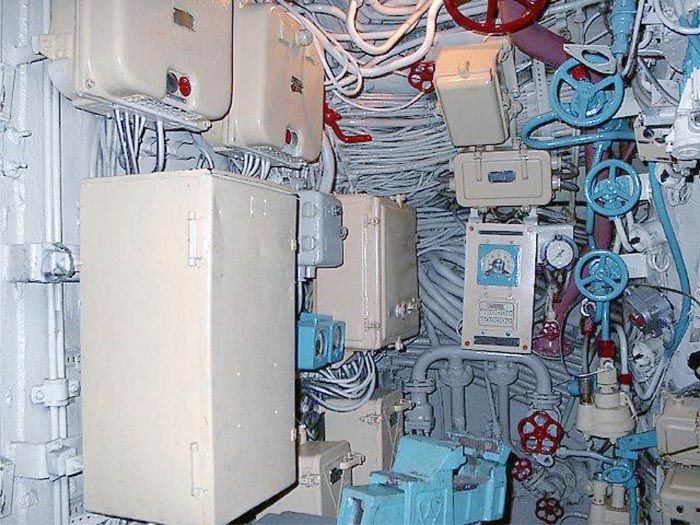
7-го ноября по приказанию из центрального поста мотористы 5-го отсека начали готовить правый дизель к пуску в режиме РДП. При проворачивании воздухом на 2-3 оборота из индикаторных кранов всех цилиндров стала выбрасываться вода, о чём старшина команды мотористов мичман А.Столяров немедленно доложил по громкоговорящей связи в центральный пост. После этого из центрального поста с помощью машинного телеграфа поступила команда - готовить к пуску на винт в режиме РДП левый дизель. При проворачивании левого дизеля воздухом, из всех индикаторных кранов шести цилиндров также стала выбрасываться вода. Из инструкции по эксплуатации технических средств мы знали, что при обнаружении воды по индикаторным кранам и клапану слива из внутренней газовой захлопки до выяснения и устранения причин поступления воды пускать дизель запрещается. Поэтому мы снова доложили в центральный пост о наличии воды в цилиндрах левого дизеля. Однако из центрального поста вновь поступила команда уже голосом по громкоговорящей связи, чтобы мы пустили левый дизель на винт в режиме РДП. Почему последовала эта команда, мы не знали. Хотя повлиять на отмену этой команды могли командир БЧ-5 инженер капитан-лейтенант Л.Г.Потапов и флагманский инженер-механик инженер-капитан 2 ранга В.В.Любимов, которые находились в центральном посту.
Согласно «Инструкции по управлению кораблем», мотористы обязаны выполнить команду из центрального поста, если она дана голосом после подачи данной команды машинным телеграфом.
Мотористы несколько раз провернули левый дизель воздухом до прекращения выбрасывания воды через индикаторные краны, после чего закрыли последние и пустили дизель. Сразу же послышался стук в районе первого цилиндра. Дизель немедленно остановили. Нам было ясно, что в 1-м цилиндре произошел гидравлический удар. Я не снимал с себя ответственности за случившееся. Упрекал себя за то, что позволил пустить дизель в данной ситуации. Однако делать нечего, пуск произведен, обратного хода нет. Доложили в центральный пост о случившемся. Подводная лодка оказалась в тяжелейшем положении, в строю остался только 3-й (средний) дизель, который не мог работать ни в режиме РДП, ни на продувание главного балласта. Да и зарядку АБ током 1-й ступени делать было невозможно. Поэтому было принято решение ввести в действие правый дизель. Организовали ремонтную бригаду из свободных от вахты мотористов. В работе ремонтной бригады я принимал непосредственное участие. Сначала вскрыли все лючки картера и проверили, не попала ли в масло вода. Затем проверили все шесть шатунов на погиб, то есть измерили расстояния между шатунами и втулками. После чего их сравнили со значениями, ранее замеренными и записанными в эксплуатационном журнале дизеля. Замечаний не обнаружили. После этого начали поочередно снимать крышки цилиндров, визуально осматривать, нет ли трещин со стороны рубашек охлаждения, после чего каждую крышку спрессовывали и ставили на свое штатное место с последующим её креплением. Вроде, процесс несложный. Но ведь каждая крышка цилиндров весит порядка 300 кг. Мотористам приходилось выполнять эту работу в стесненных условиях, при температуре в отсеке в 50°С и высокой влажности. Через неделю все крышки цилиндров были проверены, спрессованы и установлены на место. Опрессовкой проверили герметичность соединений водяного трубопровода в ресивере продувочного воздуха и рубашек цилиндров. Замечаний не было, но откуда же в цилиндрах дизеля появлялась вода?
При вскрытии спускных клапанов обнаружили, внутренние газовые захлопки бортовых дизелей оказались забиты гарью, поэтому вода через них не сливалась в трюм, а скапливалась в нижней части газоотвода перед внутренней газовой захлопкой.
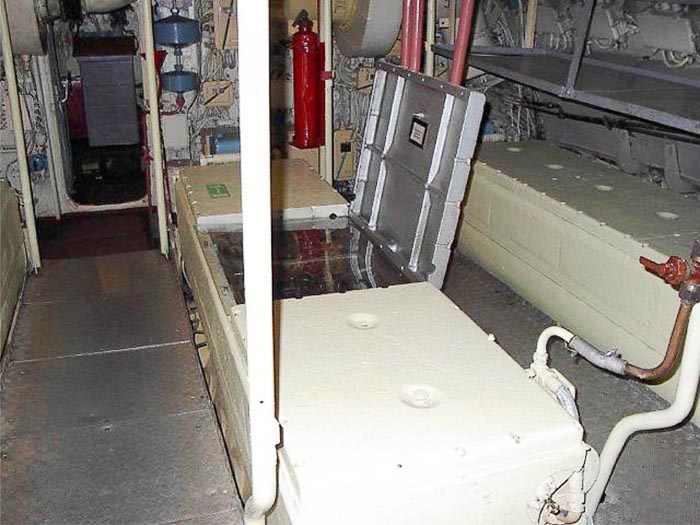
Когда же бортовые дизели поочередно готовились к пуску в режиме РДП, их проворачивали воздухом при открытых внутренних захлопках газоотвода, согласно эксплуатационной инструкции. При дифференте ПЛ на нос вода через открытую захлопку попадала в выпускной коллектор, а далее поочередно в цилиндры дизелей.
Откуда попадает забортная вода в подводном положении ПЛ в газопровод РДП мы выяснили только по возвращении в родную базу. Виновницей оказалась двухбойная газовая захлопка РДП, у которой от высокой температуры выхлопных газов работавших дизелей подгорело уплотнительное резиновое кольцо. Поэтому в закрытом положении они пропускала забортную воду, которая скапливалась в газоотводе у внутренней газовой захлопки.
Учитывая наш опыт плавания, в дальнейшем на всех подводных лодках была смонтирована система охлаждения тарелки двухбойной газовой захлопки РДП. В её открытом положении, при работе дизеля под РДП, к ней от насоса ВЦН-90 подавалась забортная вода, которая омывала резиновое кольцо, охлаждала его, и выбрасывалась газами через гусак в кормовом ограждении боевой рубки.
После недельного ремонта правого дизеля, он был опробован в работе и стал использоваться во всех режимах, что повысило техническую боеготовность ПЛ. Предварительно все спускные клапаны с газовых полостей дизелей и газоотводов были прочищены, также были проверены на проходимость спускные краники из ресивера, промежуточного колена с компенсатором, выхлопного коллектора и ресивера продувочного воздуха.
При осмотре левого дизеля было обнаружено, что шатун 1-го цилиндра имеет погиб в поперечной плоскости и касается втулки, а втулка 1-го цилиндра в нижней части имеет повреждение (отколот кусок втулки). Остальные цилиндры замечаний не имели.
На совещании, при участии инженер-капитана 2 ранга В.В.Любимова и инженер-капитан-лейтенанта А.Г.Потапова, было принято решение отремонтировать дизель для работы на 5-ти цилиндрах. Ремонт проводили свободные от вахты мотористы и привлеченные матросы из других боевых частей. Была снята крышка 1-го цилиндра, а затем с большим трудом были демонтированы поршень и шатун, так как последний своим погибом плотно прилегал к втулке. Затем откачали масло из картера дизеля, последний насухо протерли ветошью через вскрытый люк фундаментальной рамы в районе 1-го цилиндра.
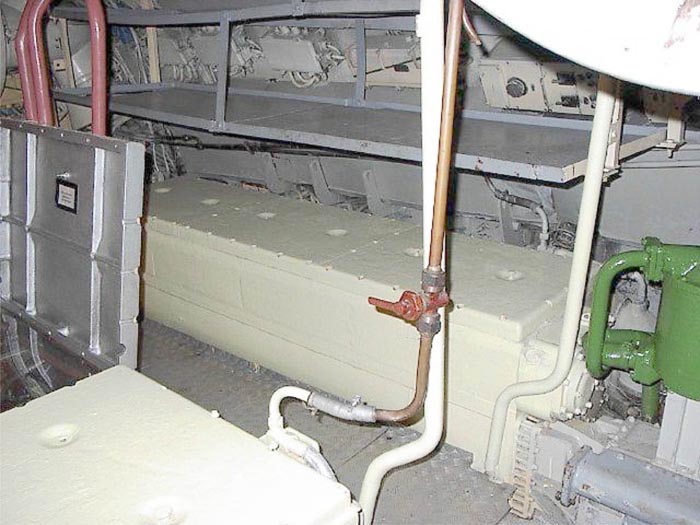
После этого, через вскрытый люк, матросы поочередно скругляли острые кромки втулки в районе отколотого куска с помощью напильника. Это делалось для того, чтобы при движении поршня его маслосъемные кольца не касались острых кромок втулки и не ломались. Это была трудоемкая операция, так как чугунная втулка цилиндра поддавалась обработке с большим трудом.
Через неделю подготовительная работа была закончена, из ЗИПа был взят новый шатун, к которому подсоединили поршень, предварительно сняв с него два нижних маслосъемных кольца, так как они могли, при движении поршня вниз, достать до отколотого куска втулки и поломаться.
Поршень с шатуном опустили во втулку цилиндра, после чего смонтировали нижнюю головку шатуна к шатунной шейке коленчатого вала. Затем поставили на место и закрепили крышку цилиндра, очистили картер дизеля от посторонних предметов, последний заполнили маслом и прокачали масляным насосом. После этого закрыли крышку люка фундаментальной рамы. Насос-форсунку 1-го цилиндра отключили от подачи топлива. Дизель еще раз тщательно проверили, провернули его вручную и воздухом и оставили его в резерве, решив его эксплуатировать в том случае, если из строя выйдет один из двух работавших дизелей.
При вводе в строй дизелей отличились все матросы, которые участвовали в этом процессе, но особенно хочу отметить высокую работоспособность старшины команды мотористов мичмана А.Столярова, командиров отделений мотористов старшин 1 статьи А.Ефремова, Е.Николаева, С.Некрасова, старших мотористов старших матросов А.Миловидова, Н.Никитина.
Это действительно мастера своего дела, специалисты высокого класса.
Продолжение следует.